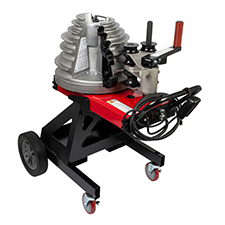
Understanding Electrical Conduits and Their Associated Bending Tools
Steve Maurer, IME
Electrical installations require an understanding of various components, chief among them being electrical conduits and the tools used to shape them. This article aims to shed light on the different types of rigid electrical conduit and the appropriate bending tools required for each.
Rigid Metal Conduit (RMC)
RMC is a thick, heavy-duty conduit constructed from steel or aluminum. It's widely employed in commercial and industrial settings, providing a high level of protection, particularly in areas exposed to potential physical damage. To bend RMC, a heavy-duty mechanical or hydraulic conduit bender is necessary due to the material's tough construction. These benders exert a significant amount of force to create a bend without damaging the conduit.
Intermediate Metal Conduit (IMC)
IMC, like RMC, is made from steel or aluminum but is lighter and easier to work with. It's favored for installations where the conduit needs to be buried or encased in concrete. Despite being less robust than RMC, IMC still requires a heavy-duty mechanical or hydraulic conduit bender to shape it without causing kinks or breaks.
Electrical Metallic Tubing (EMT)
EMT is a popular choice for indoor applications in commercial buildings and some residential applications due to its thin walls and easy bending characteristics. A manual conduit bender is sufficient for shaping EMT. These hand tools, constructed from sturdy metals like steel or iron, often come with a foot pedal for leverage. A ratchet style bender has different sized grooves for various conduit diameters, and the conduit is bent by placing it in the appropriate groove and applying force with a foot pedal or bar.
Rigid Polyvinyl Chloride Conduit (PVC)
PVC conduit is a lightweight, cost-effective alternative, resistant to corrosion and abrasion, making it suitable for underground installations or areas with corrosive materials. Unlike metal conduits, PVC is not bent with a traditional conduit bender. Instead, it's heated until it becomes pliable, bent into the desired shape, and then allowed to cool and harden. This process can be achieved with a specialized PVC heating blanket or box or with a cautious application of a heat gun.
Understanding the right conduit and bending tool for the job is crucial in electrical installations. It ensures the safety, durability, and efficiency of the electrical system. However, bending conduit—especially RMC, IMC, EMT, and PVC—requires skill and knowledge to do correctly. Improper bending can damage both the conduit and the wiring inside, and may lead to safety hazards. Therefore, it's always a good idea to have conduit bent by a trained professional or under the guidance of one.
Done Right, Bending Conduit Saves Time and Money and Ensures Compliance
Conduit bending is not just a matter of aesthetics or convenience; it's also a matter of compliance with electrical codes and safety regulations. The National Electrical Code (NEC), which sets the standard for electrical safety in the United States, has specific rules about conduit bends. For example, according to the NEC, the total number of bends between pull points—such as junction boxes or fittings—cannot exceed 360 degrees. This limit helps ensure that the wires can be pulled through the conduit without excessive force, which could damage the wires or the conduit.
Additionally, the NEC specifies minimum radius requirements for bends to prevent damage to the conduit and the enclosed wires during bending. The bend radius varies depending on the type and size of the conduit. For example, for 1/2-inch EMT, the minimum radius is 4 inches. Always refer to the NEC or your local building codes for the specific requirements in your area. Proper bending is not only crucial for the successful installation of the conduit but also for the safety and longevity of the electrical system.
Another advantage of bending conduit is the capability to avoid extra fittings and connections. Applying bends in a conduit can remove the need for unnecessary condulets and connections, which can lead to time and cost savings, reduce potential points of failure, and result in a cleaner, more professional-looking installation. However, be sure to understand the standards and regulations for entry fittings for pulling points, usually governed by conduit run length.
Conduit Bending is an Important Part of the Job
Bending conduit is an indispensable aspect of numerous electrical installations due to a variety of factors. One primary reason is to route around obstacles. Buildings and other structures are laden with potential obstacles such as walls, beams, and other utilities like plumbing pipes and HVAC ducts. Bending conduit allows electricians the flexibility to navigate around these obstacles, enabling them to steer the wiring to its intended destination.
Conduit bending isn’t just grunt work. It was one of the first things I had to learn and practice. My trainer didn’t allow poorly formed bends and offsets, even if hidden by ceiling tiles. A good looking run of conduit shows a certain pride in your work.
Rigid Metal Conduit (RMC)
RMC is a thick, heavy-duty conduit constructed from steel or aluminum. It's widely employed in commercial and industrial settings, providing a high level of protection, particularly in areas exposed to potential physical damage. To bend RMC, a heavy-duty mechanical or hydraulic conduit bender is necessary due to the material's tough construction. These benders exert a significant amount of force to create a bend without damaging the conduit.
Intermediate Metal Conduit (IMC)
IMC, like RMC, is made from steel or aluminum but is lighter and easier to work with. It's favored for installations where the conduit needs to be buried or encased in concrete. Despite being less robust than RMC, IMC still requires a heavy-duty mechanical or hydraulic conduit bender to shape it without causing kinks or breaks.
Electrical Metallic Tubing (EMT)
EMT is a popular choice for indoor applications in commercial buildings and some residential applications due to its thin walls and easy bending characteristics. A manual conduit bender is sufficient for shaping EMT. These hand tools, constructed from sturdy metals like steel or iron, often come with a foot pedal for leverage. A ratchet style bender has different sized grooves for various conduit diameters, and the conduit is bent by placing it in the appropriate groove and applying force with a foot pedal or bar.
Rigid Polyvinyl Chloride Conduit (PVC)
PVC conduit is a lightweight, cost-effective alternative, resistant to corrosion and abrasion, making it suitable for underground installations or areas with corrosive materials. Unlike metal conduits, PVC is not bent with a traditional conduit bender. Instead, it's heated until it becomes pliable, bent into the desired shape, and then allowed to cool and harden. This process can be achieved with a specialized PVC heating blanket or box or with a cautious application of a heat gun.
Understanding the right conduit and bending tool for the job is crucial in electrical installations. It ensures the safety, durability, and efficiency of the electrical system. However, bending conduit—especially RMC, IMC, EMT, and PVC—requires skill and knowledge to do correctly. Improper bending can damage both the conduit and the wiring inside, and may lead to safety hazards. Therefore, it's always a good idea to have conduit bent by a trained professional or under the guidance of one.
Done Right, Bending Conduit Saves Time and Money and Ensures Compliance
Conduit bending is not just a matter of aesthetics or convenience; it's also a matter of compliance with electrical codes and safety regulations. The National Electrical Code (NEC), which sets the standard for electrical safety in the United States, has specific rules about conduit bends. For example, according to the NEC, the total number of bends between pull points—such as junction boxes or fittings—cannot exceed 360 degrees. This limit helps ensure that the wires can be pulled through the conduit without excessive force, which could damage the wires or the conduit.
Additionally, the NEC specifies minimum radius requirements for bends to prevent damage to the conduit and the enclosed wires during bending. The bend radius varies depending on the type and size of the conduit. For example, for 1/2-inch EMT, the minimum radius is 4 inches. Always refer to the NEC or your local building codes for the specific requirements in your area. Proper bending is not only crucial for the successful installation of the conduit but also for the safety and longevity of the electrical system.
Another advantage of bending conduit is the capability to avoid extra fittings and connections. Applying bends in a conduit can remove the need for unnecessary condulets and connections, which can lead to time and cost savings, reduce potential points of failure, and result in a cleaner, more professional-looking installation. However, be sure to understand the standards and regulations for entry fittings for pulling points, usually governed by conduit run length.
Conduit Bending is an Important Part of the Job
Bending conduit is an indispensable aspect of numerous electrical installations due to a variety of factors. One primary reason is to route around obstacles. Buildings and other structures are laden with potential obstacles such as walls, beams, and other utilities like plumbing pipes and HVAC ducts. Bending conduit allows electricians the flexibility to navigate around these obstacles, enabling them to steer the wiring to its intended destination.
Conduit bending isn’t just grunt work. It was one of the first things I had to learn and practice. My trainer didn’t allow poorly formed bends and offsets, even if hidden by ceiling tiles. A good looking run of conduit shows a certain pride in your work.
Photo courtesy of Gardner Bender