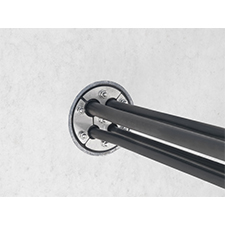
Sealant Options for Safer Conduits
Chuck Ross
Conduit provides a protective passageway for electrical and data cables. Unfortunately, it also can provide a passageway for moisture and hazardous and/or explosive gases to move from one area of a facility to another, as well. That’s why the National Electrical Code (NEC) requires conduit to be sealed in certain locations. Knowing where sealing is required and what options are the most reliable are key to ensuring both code compliance and system safety over the life of an installation.
Conduit sealing is required in the following applications:
Mastic putty is one option contractors can turn to in low-voltage or non-hazardous settings, but it can fall short in providing necessary protection in more critical applications. Over time, cracking and sagging can create gaps through which moisture and gases can penetrate. Where performance is more critical, foam or mechanical sealants can provide the needed protection.
Closed-cell foam is available as a spray or in pre-formed sheets, making it easy to install. It conforms to the shape of the conduit and fills any gaps. It also provides good thermal insulation, preventing heat transfer and helping to maintain consistent temperatures inside the conduit. It does require curing time, though, which can impact construction schedules. And it also creates a solid, continuous barrier, which can make future modifications difficult.
Mechanical sealants, which can take several forms, are easier to remove and reinstall, so future maintenance efforts can be easier than with foam. This kind of versatility can be especially useful in projects like data centers, where rapid technology advances are more likely to lead to facility upgrades over time. However, thermal insulation might not be as consistent with mechanical fittings as it is with foam.
Conduit sealing is required in the following applications:
- Wet locations. Conduit located in wet or damp environments, including underground installations, in wet areas or where it will be exposed to water. In this case, sealing helps protect electrical conductors from water damage and potential short circuits.
- Hazardous locations. These include settings where flammable gases, vapors or combustible dusts are present. Here, sealing prevents these hazards from migrating throughout a facility, reducing the risk of explosions or fires.
- Sealed systems. Conduit used for environmental air handling, dust collection and other similar applications may require sealing to maintain system integrity and prevent contamination.
Mastic putty is one option contractors can turn to in low-voltage or non-hazardous settings, but it can fall short in providing necessary protection in more critical applications. Over time, cracking and sagging can create gaps through which moisture and gases can penetrate. Where performance is more critical, foam or mechanical sealants can provide the needed protection.
Closed-cell foam is available as a spray or in pre-formed sheets, making it easy to install. It conforms to the shape of the conduit and fills any gaps. It also provides good thermal insulation, preventing heat transfer and helping to maintain consistent temperatures inside the conduit. It does require curing time, though, which can impact construction schedules. And it also creates a solid, continuous barrier, which can make future modifications difficult.
Mechanical sealants, which can take several forms, are easier to remove and reinstall, so future maintenance efforts can be easier than with foam. This kind of versatility can be especially useful in projects like data centers, where rapid technology advances are more likely to lead to facility upgrades over time. However, thermal insulation might not be as consistent with mechanical fittings as it is with foam.
Photo courtesy of American Polywater